According to the specific situation of the truss, it should first be broken down into several parts as much as possible, and the Truss Beam Welding Machine is used for internal processing and welding. After completion, it will be transported to the truss for on-site assembly and welding.
In the process of assembly and welding, the formation of internal stress should be minimized to reduce welding deformation. According to the analysis of the drawings, the process flow should be formulated according to this principle. If the welding current is properly controlled, the current cannot be too large. Welding seams can be prevented according to the requirements of the drawings. Internal stress and deformation are two pairs of contradictory things. If the stiffness is not large, the small deformation should be controlled. If the rigidity is large, the stress during the assembly and welding process should be mainly controlled.
The truss is a stress structure. Therefore, we recommend using DC welding with high-quality electrodes and reverse polarity connections.
Before welding, remove rust, degreasing, dehumidifying and baking as required. There are many fillet welds in the truss. Butt welds must be open and double-sided to ensure penetration and increase in height.
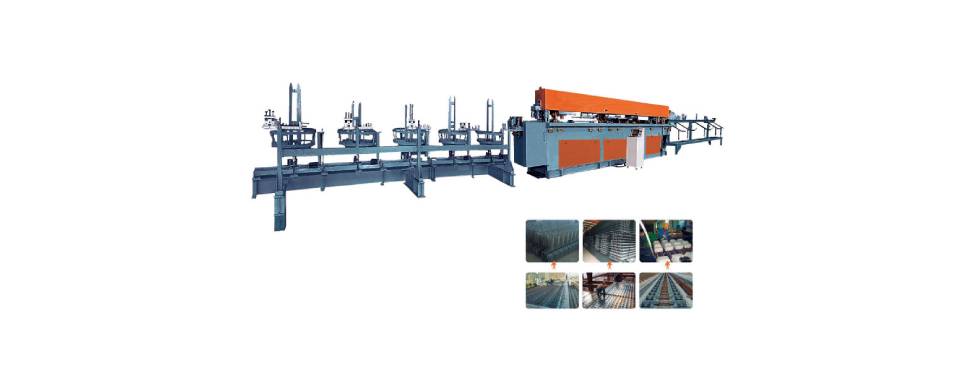
The new High-Precision Truss Beam Welding Machine production line has four technical characteristics:
- The new straightening device improves the straightness of the truss product, and improves the integrity and stability of the equipment.
- The roll straightness can be adjusted according to the diameter of different steel bars. It can not only reduce noise, but also avoid damage to the surface of the steel bar during the straightening process.
- The wire feeding mechanism replaces the sensing device. The start-stop induction device uses an alloy copper block to replace the traditional induction switch, which can extend the service life and reduce the accident rate of the equipment.
- Upgrade the shearing machine. Using an electric camshaft to drive the cutter cutting tool can prolong the service life of the cutter, there is no hydraulic leakage problem, and reduce the failure rate and maintenance cost. The improvement of these four technical nodes provides a fundamental guarantee for improving the efficiency of the production line.
If you have more questions, please contact the Truss Girder Welding Machine Supplier