Rebar bending machine, one of rebar processing machinery. The working mechanism is a horizontal working disc that rotates on a vertical axis. The steel bar is placed in the dotted line in the figure. The support pin is fixed on the machine tool. The center pin and the bending pin are mounted on the working disc. The disc rotates At that time, the rebar is bent. In order to bend steel bars of various diameters, there are several holes in the working plate for inserting bending pin shafts, and the center pin shafts of different diameters can also be replaced accordingly. The Stirrup Bender is designed for straightening, bending and cutting on one machine.
The rebar bending machine belongs to an improvement of the structure of the rebar bending machine. The utility model includes a reducer and a large gear. The pinion gear and the curved disc surface are characterized by the structure: the two-stage brake motor is directly connected with the reducer for first-level deceleration; the small gear meshes with the large gear for two-level deceleration; the large gear always drives the curved disc surface to rotate; the curved disc surface is provided There are a central axis hole and a number of curved axis holes; a number of positioning axis holes are respectively provided on the positioning square bar of the worktable. Because the two-stage brake motor is directly connected with the reducer for one-stage deceleration, the input and output revolution ratios are accurate, the bending speed is stable and accurate, and the automatic conversion speed can be controlled by electric, and the brake can ensure the bending angle. Using the positive and negative rotation of the motor, the rebar is bent in two directions. The central axis can be replaced for easy maintenance. Intelligent control can be used.
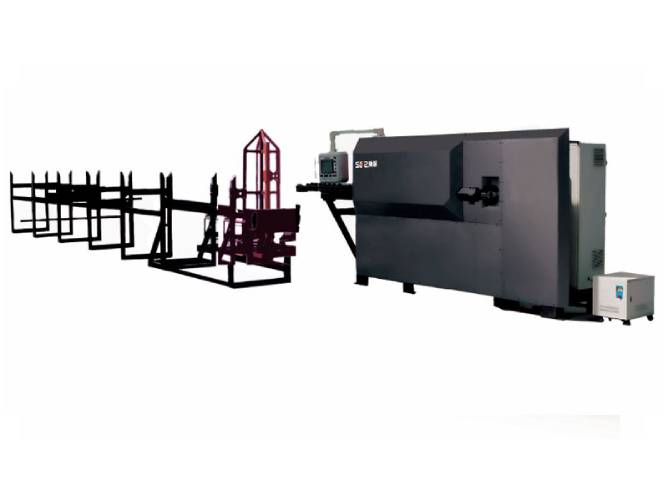
What are the precautions when using a bending machine such as the Easy Operate Stirrup Bending Machine? Let’s follow the Fast Processing Stirrup Bending Machine Manufacturer that can process Mair quickly. During the operation, insert the bent end of the steel bar into the gap provided by the turntable, and fix the other end against the fuselage and press it by hand. Check the fixation of the fuselage and ensure that it is installed on the side blocking the steel bar before it can be started. During the operation, it is strictly forbidden to replace the mandrel, change the angle, adjust the speed and other operations, and do not add oil or remove it. When bending steel bars, it is strictly forbidden to process the steel bar diameter, number and mechanical speed specified by the machine. When bending high-hardness or low-alloy steel bars, the maximum limit diameter should be changed according to the mechanical nameplate, and the corresponding core should be replaced.
What are the requirements during the operation? Safety requirements for manual bending forming When bending thick steel bars with a horizontal spanner, pay attention to grasp the essentials of operation, the heels must stand firm, the two feet stand in lunges, set up the board, pay attention to the board saw, the board mouth is locked to the steel bar, the bending force Slow, don’t use too much force to prevent the board from being pulled off and people being thrown down. It is not allowed to bend thick steel bars in high places or on scaffolding, to avoid falling in high places due to disengagement during operation.
Safety requirements for mechanical bending. Before the formal operation of the machine, all parts of the machine should be checked, and the no-load test operation is normal before it can be officially operated. Attention should be focused during operation, familiar with the direction of work circling, the placement of rebar should match the direction of rotation of the frame and the work plate, and can not be reversed. During operation, the rebar must be placed in the middle and lower part of the plug. It is strictly forbidden to bend the steel bar that exceeds the cross-sectional size. The direction of rotation must be accurate. The distance between the hand and the plug must not be less than 200mm. During the mechanical operation, it is forbidden to refuel and clean, and it is strictly forbidden to replace the mandrel, pin and change the angle. If you are interested, please contact us.